Automatic dosing and storage of raw materials
- Weighting systems: Micro, Minor, Macro raw materials
- Automatic warehouse: 38 shelves of 6 boxes each. A total of 228 positions
- Moveable weight station: For accurate picking from the automatic warehouse
- Automatic box feeder: Tray for 18 boxes
WEIGHING SYSTEM
To achieve maximum variability in the automatic weighing process, we produce scales in several designs. Both the method of dosing and the size of the reservoir differ. Weighing itself is provided by a worm gear controlled by a frequency converter. Weighing benches are equipped with sensitive strain gauges communicating via CAN Open with minimal response.
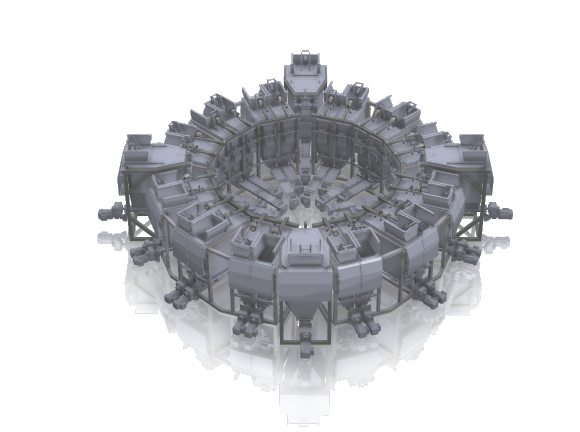

Storage of raw materials
Before actually pouring the raw material into the hopper, the bar code of the raw material and the hopper must be read. If the compatibility of the raw materials is evaluated, the lid is released and the raw material can be received.VERTICAL STORAGE SYSTEM WITH CONTROLLED WEIGHING
The automatic warehouse is used for the storage of low-volume raw materials and their mixtures. Mixtures of micro raw materials are weighed semi-automatically using a mobile weighing bench, which is located at the shelf feeder. The automatic warehouse extends the shelves with the required raw material according to the recipe, the actual weighing of the required weight is carried out by the machine operator. The weighed mixture can be stored back in the automatic warehouse or in the automatic dumper for production. Each position is equipped with a POKA-YOKE pass- through sensor as a prevention against mixing up the raw material.
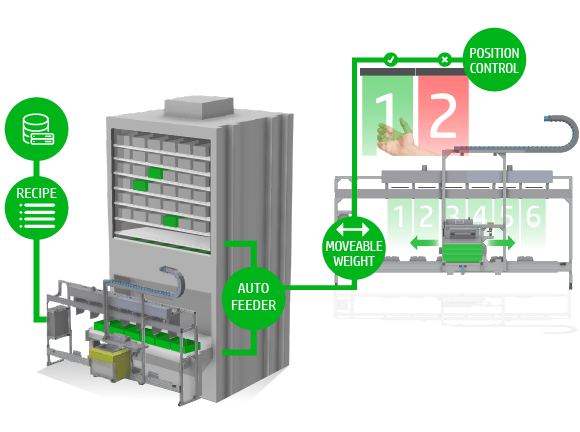

Stocking of raw materials in an automatic warehouse
Before the raw material is poured into the container, the bar code of the raw material and the box must be read. If the compatibility of the raw materials is evaluated, the scale is released and the raw material can be received. In the receiving station, the amount of raw material is entered into the SQL database. The automatic warehouse selects an empty position for storage and also writes information about the position of the box into the SQL database.AUTOMATIC BOX FEEDER
The linear feeder ensures the transport of the box from three tracks. Each track serves as a stack of 6 boxes. When the box is stored in the dumper, the barcode is read, thereby ensuring an overview of the contents and position of each box. When a raw material is requested, the manipulator automatically selects a path with the correct raw material and dumps its contents into the hopper.
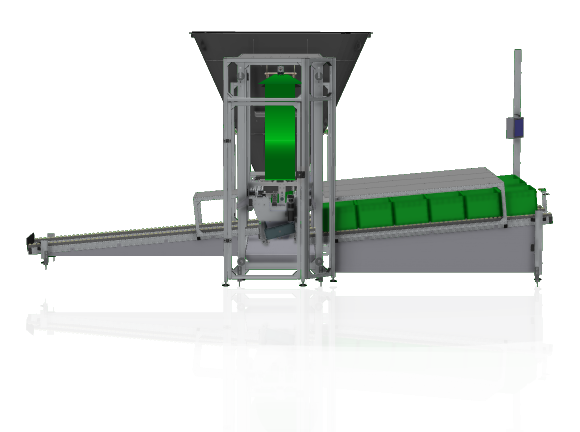
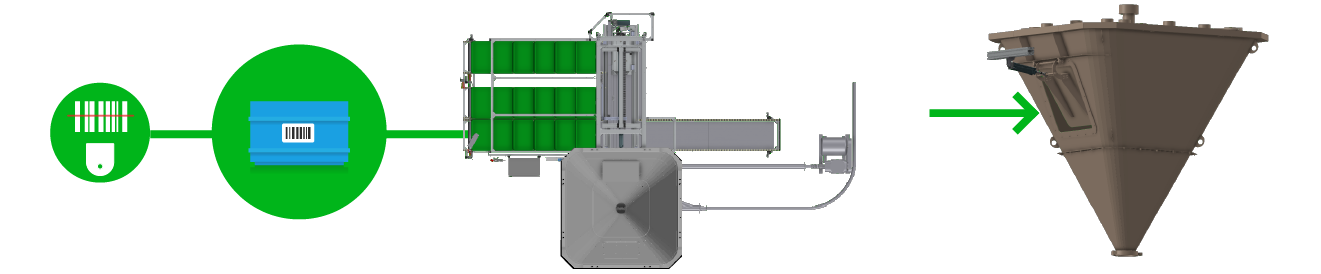
Storage of boxes in the feeder
The barcode is read the first time when entering the lane and the second time when it is taken over by the manipulator. Information about the contents of the box is stored in an SQL database.Packaging line with robotic palletization
- Platform: For maximum use of space, the line is situated on the floor
- Spiral conveyor
- Robotic palletizing Equipped with FANUC robots
- Inclined conveyor with crasher
Inclined conveyor with crasher
The products are moved along the inclined conveyor to the manual station on the platform. The conveyors are equipped with a crasher that squeezes excess air out of the package.
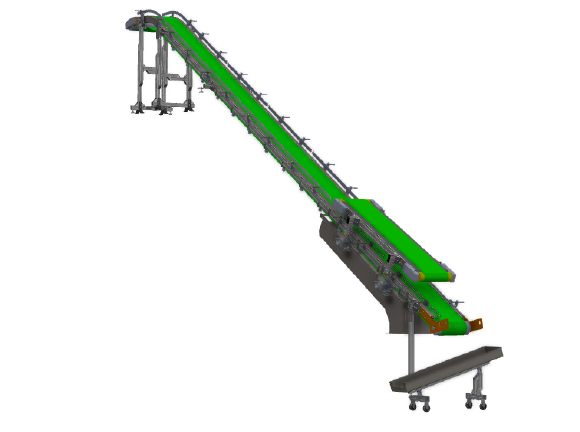
Spiral conveyor
A spiral conveyor with a modular belt enabling inter-floor transport of the product.
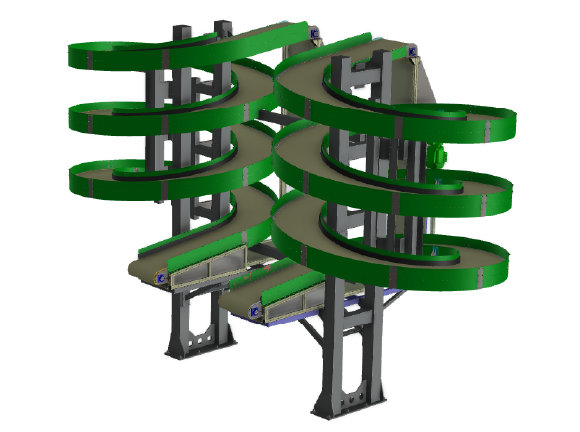
Robotic palletization
Fully automatic palletizing system. When the product is changed, the packaging copy is loaded according to which the robot places the products on the pallet.
